Create tools.
Manage tools.
Maintain tools
with the tool management twinio.
No My tapio company account yet?
No My tapio company account yet?
No My tapio company account yet?
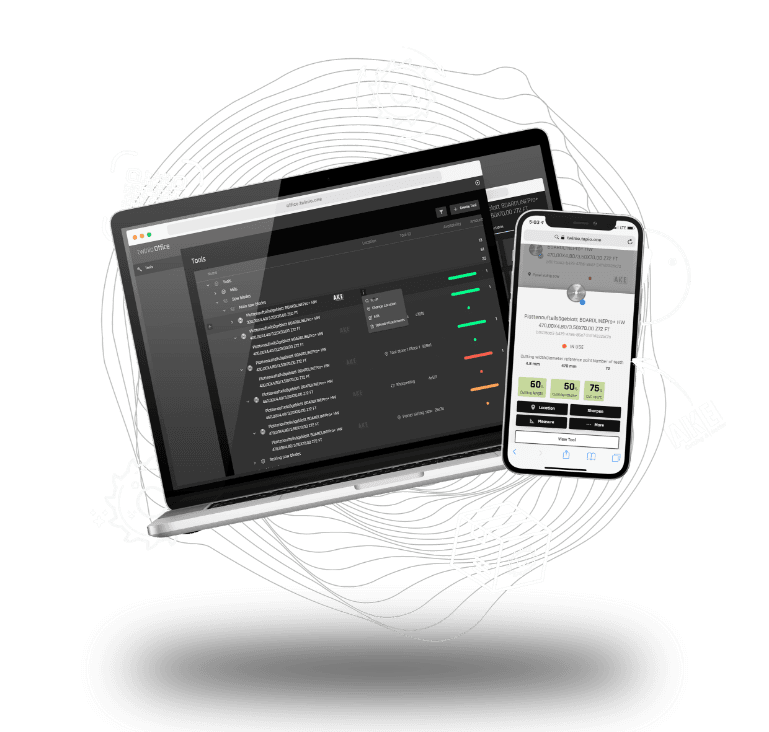
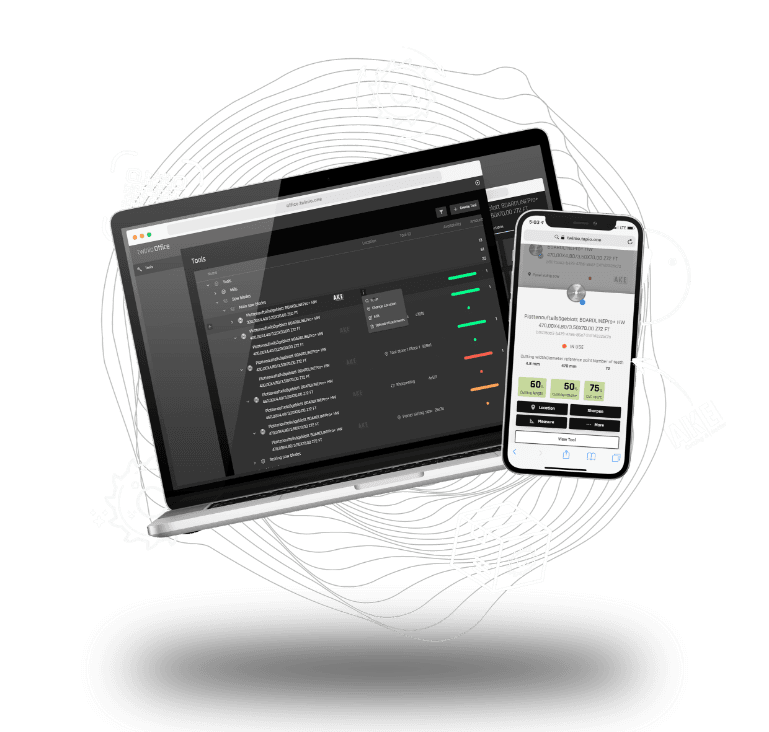
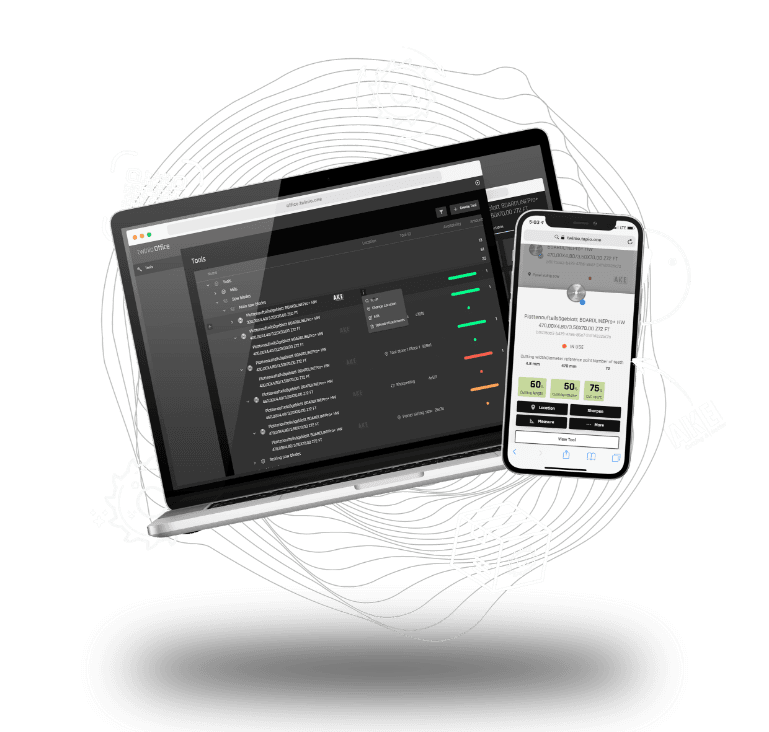
Manage tools
Manage tools easily and digitally
Scan your tools, receive original data from top manufacturers and retain full control. Your digital tool, always with you, no matter when and where - for maximum transparency and efficiency in your workshop.
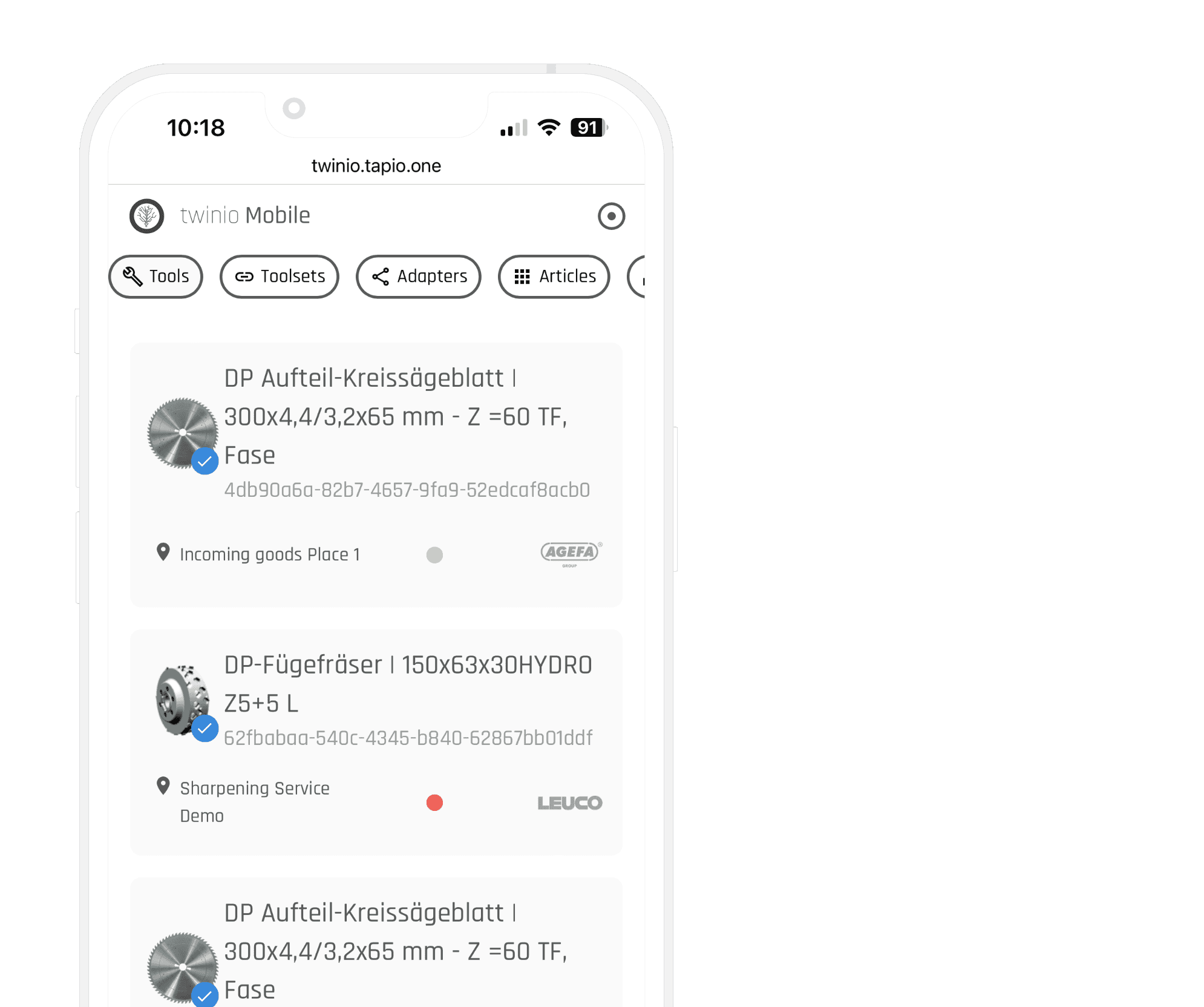
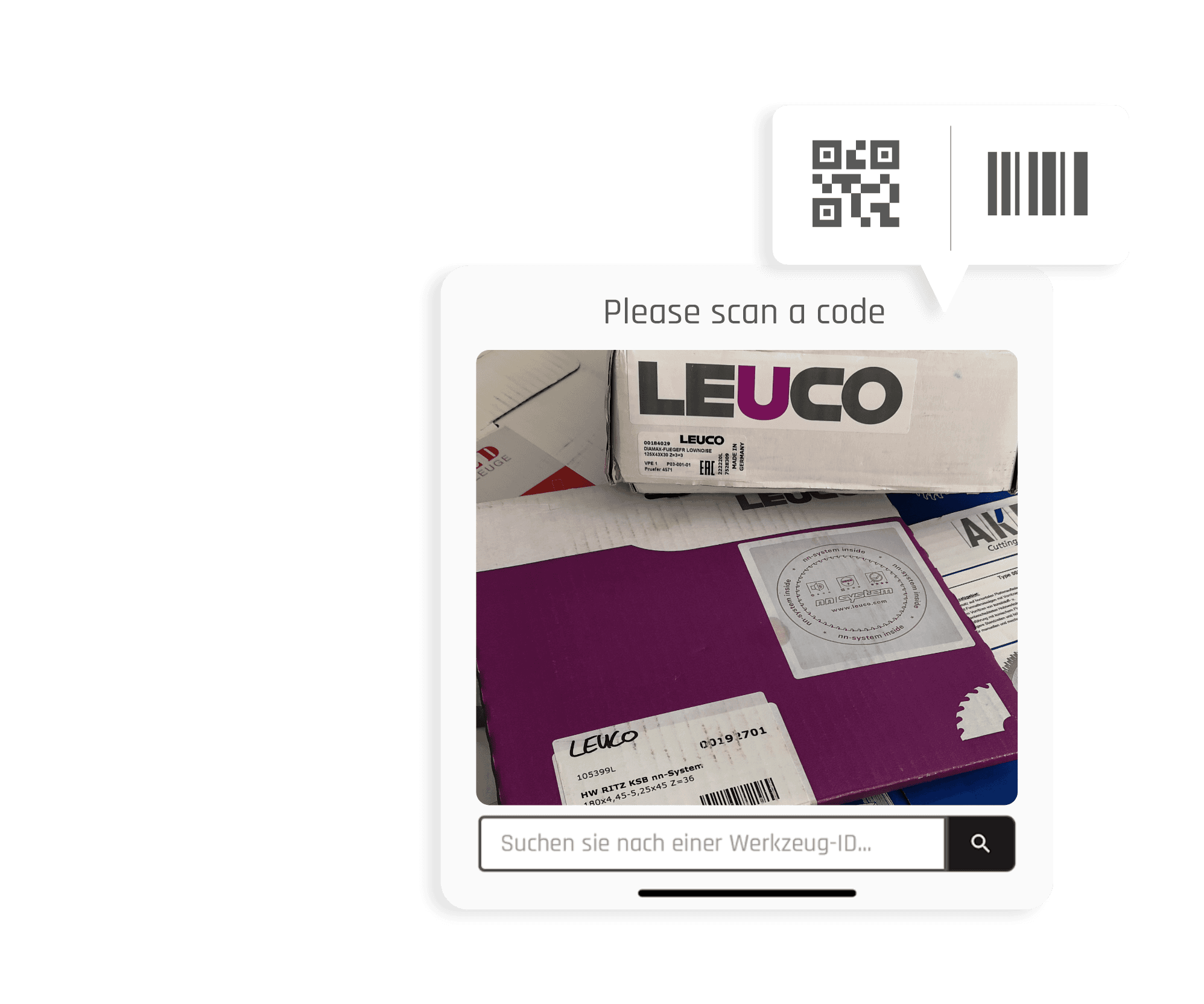
Manage tools
Manage tools easily and digitally
Scan your tools, receive original data from top manufacturers and retain full control. Your digital tool, always with you, no matter when and where - for maximum transparency and efficiency in your workshop.
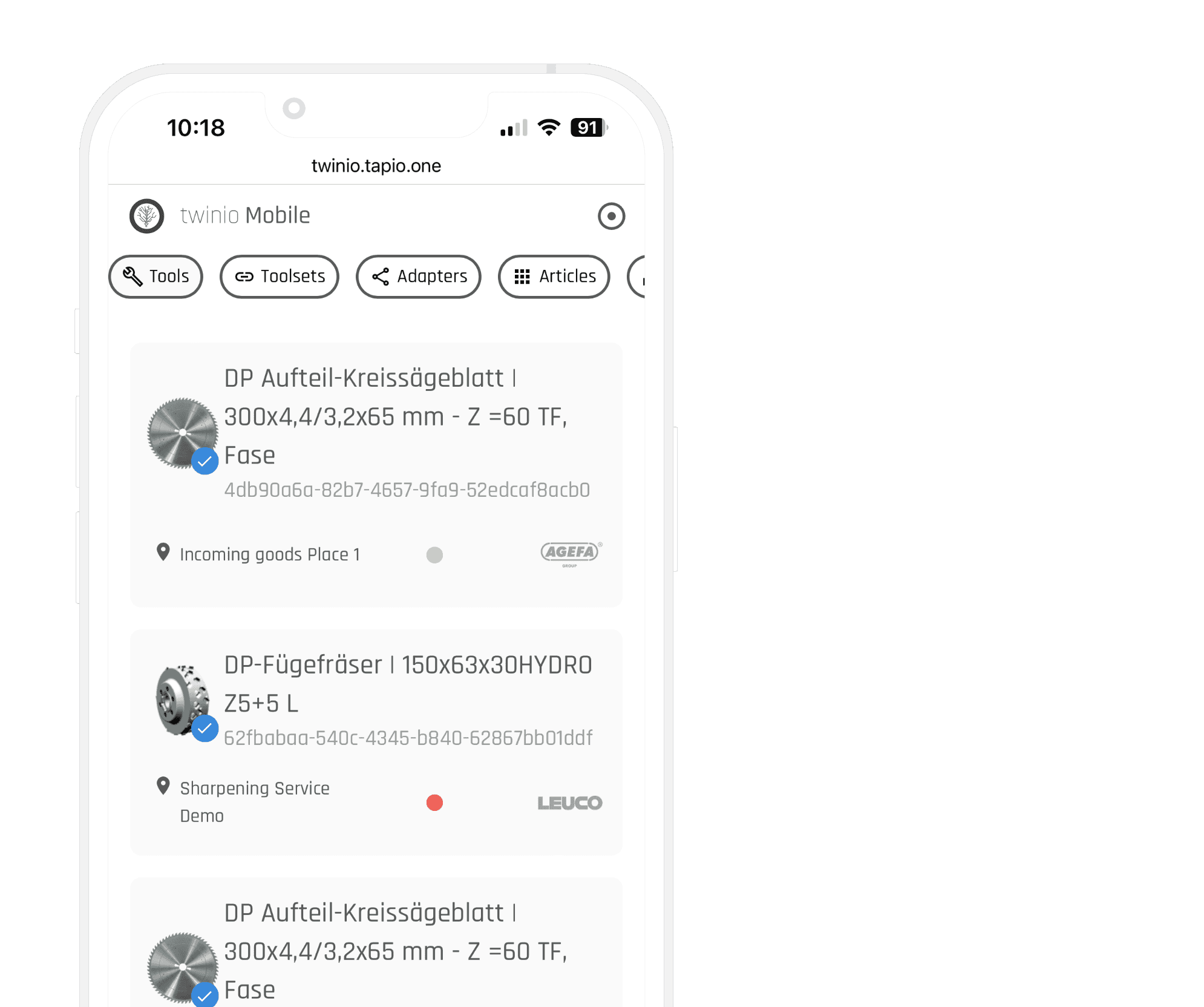
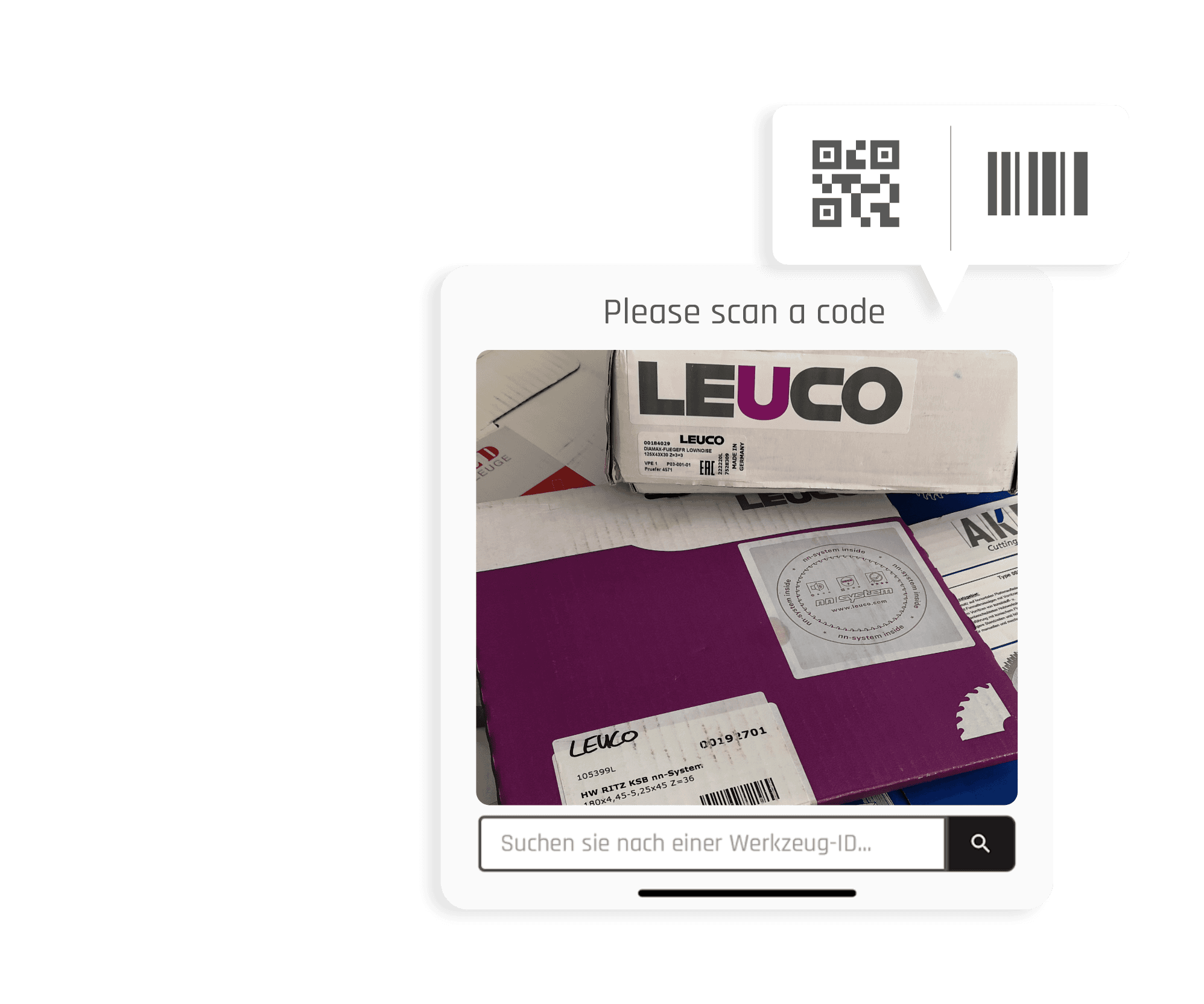
Manage tools
Manage tools easily and digitally
Scan your tools, receive original data from top manufacturers and retain full control. Your digital tool, always with you, no matter when and where - for maximum transparency and efficiency in your workshop.
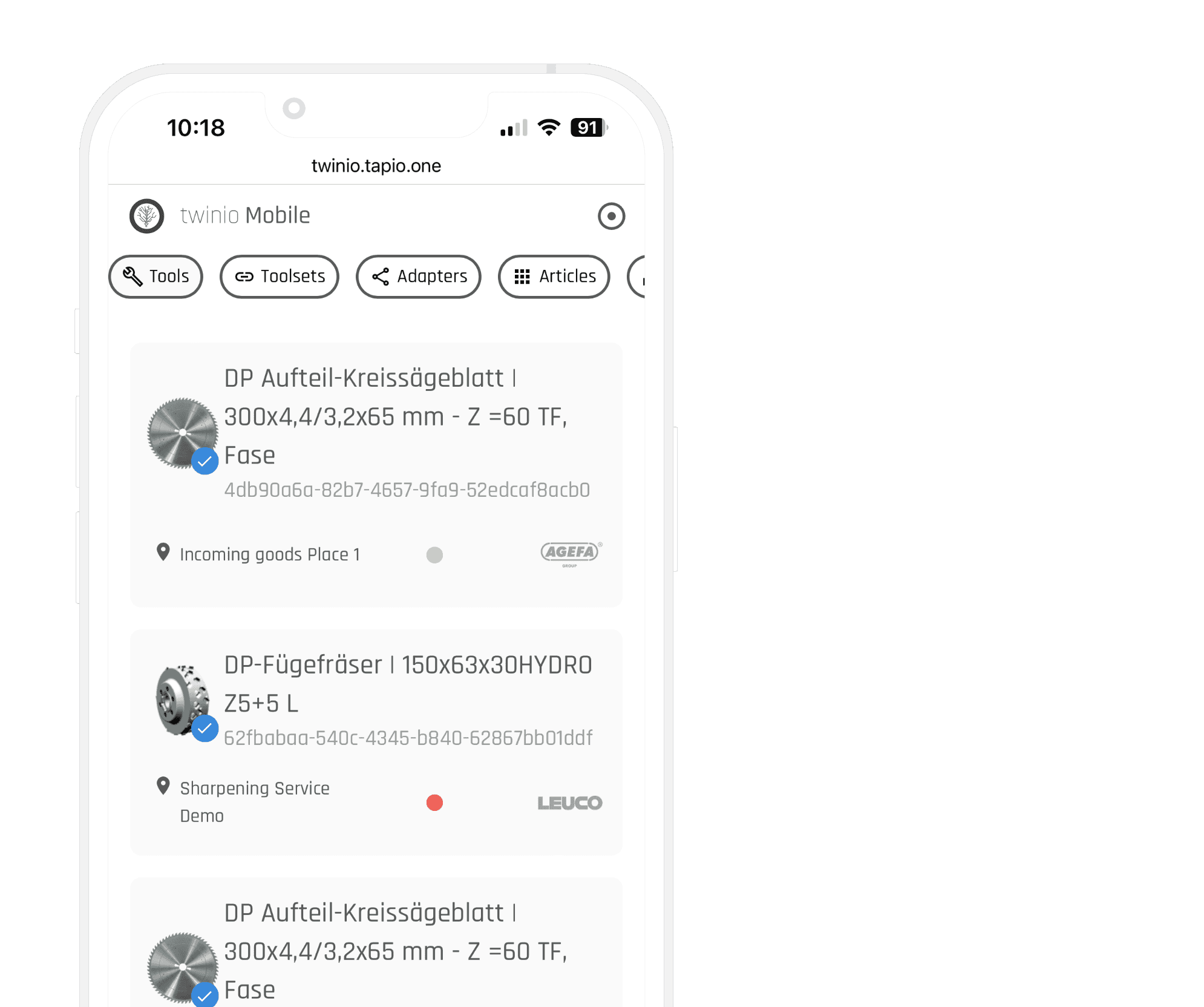
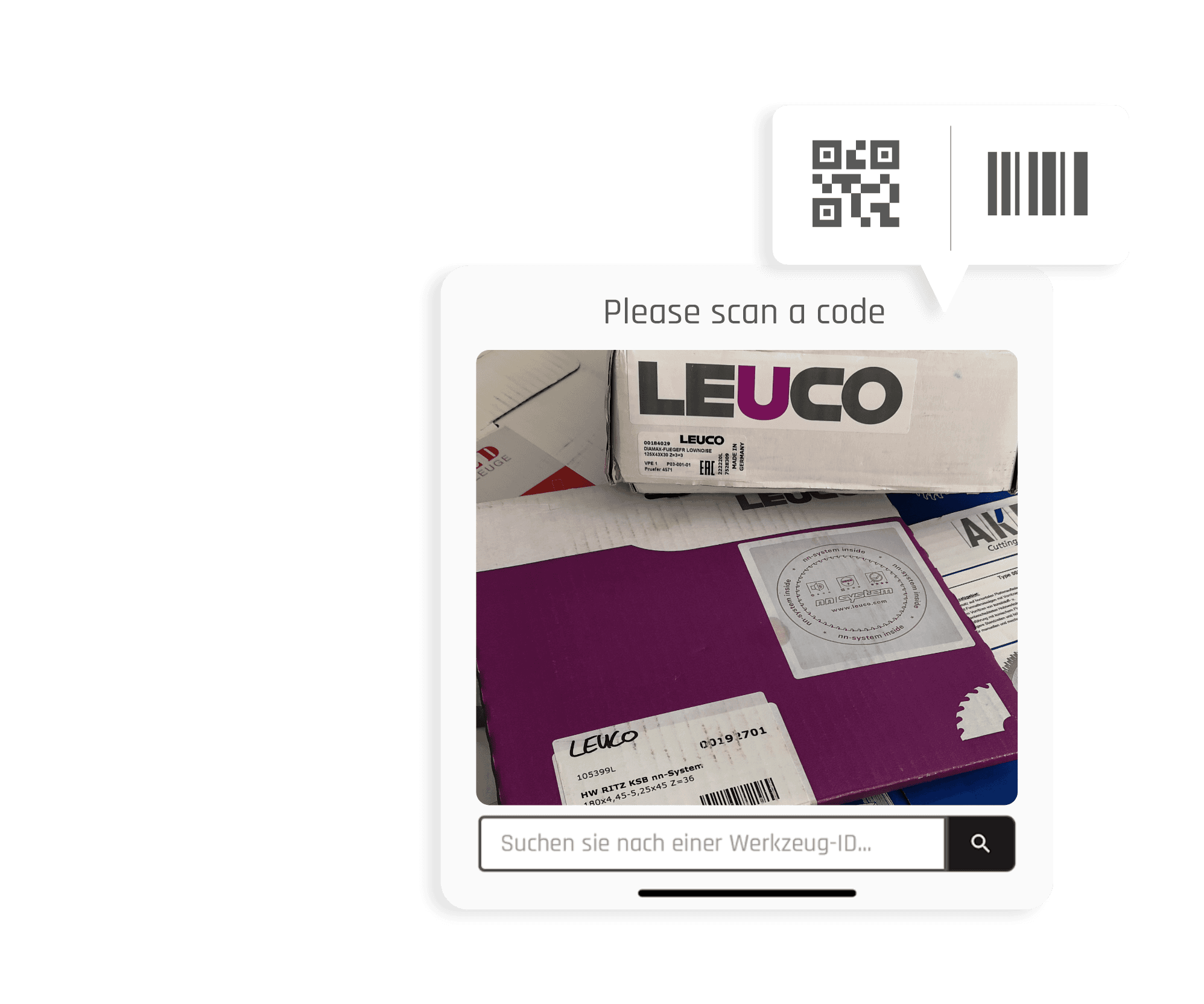
Use tools
Save time through machine connectivity
Maximize efficiency and precision through seamless machine connectivity. Record the performance of your tools directly via twinio by automatically providing your machine with up-to-date and relevant tool data. Save valuable time and optimize your workflow.
Use tools
Save time through machine connectivity
Maximize efficiency and precision through seamless machine connectivity. Record the performance of your tools directly via twinio by automatically providing your machine with up-to-date and relevant tool data. Save valuable time and optimize your workflow.
Use tools
Save time through machine connectivity
Maximize efficiency and precision through seamless machine connectivity. Record the performance of your tools directly via twinio by automatically providing your machine with up-to-date and relevant tool data. Save valuable time and optimize your workflow.
Sharpen tools
Sharpening made digital
Tool maintenance made easy: Select a sharpening service in twinio, create orders and track the process. The new measurement data is available to you immediately after sharpening. Rediscover efficiency.
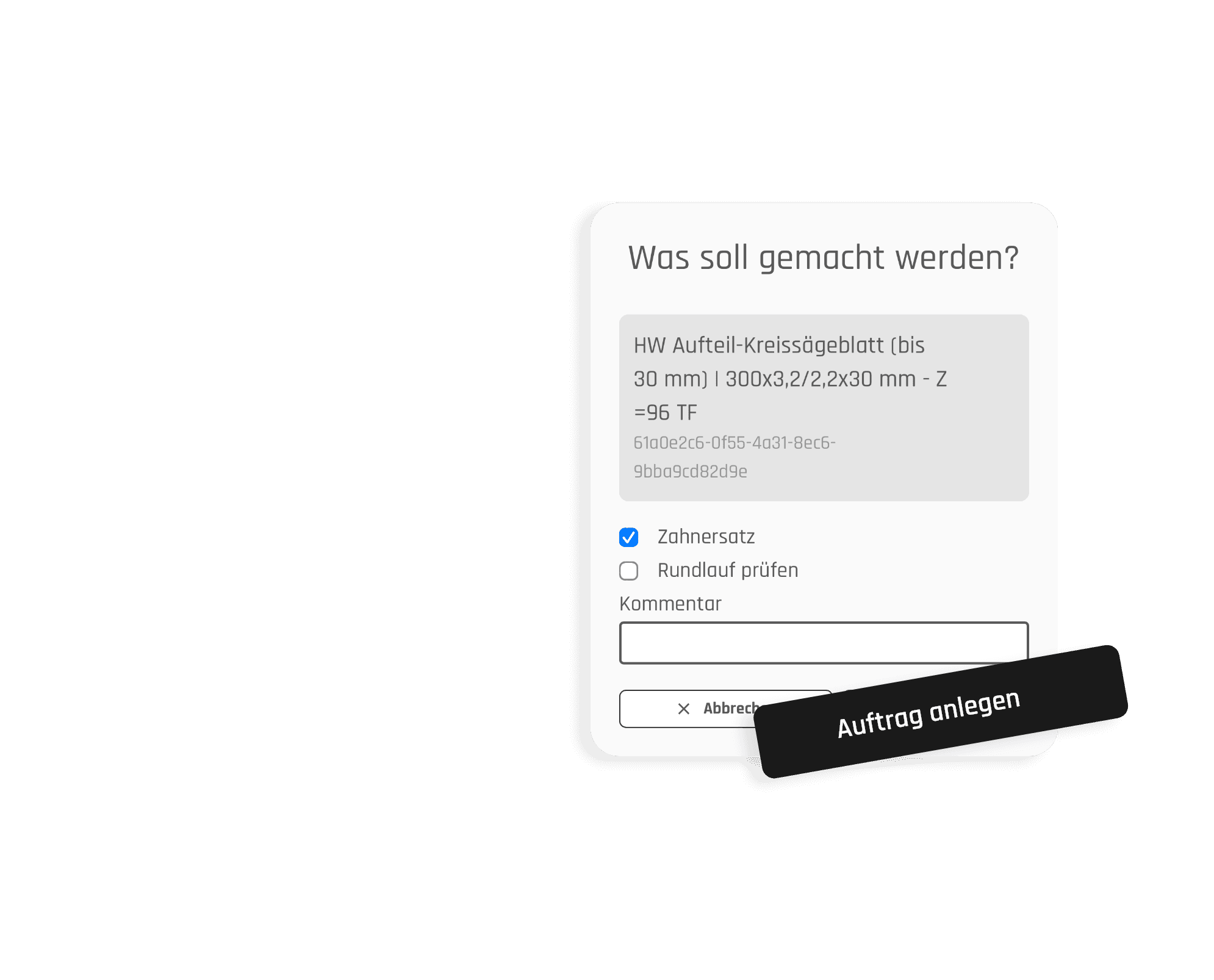
Sharpen tools
Sharpening made digital
Tool maintenance made easy: Select a sharpening service in twinio, create orders and track the process. The new measurement data is available to you immediately after sharpening. Rediscover efficiency.
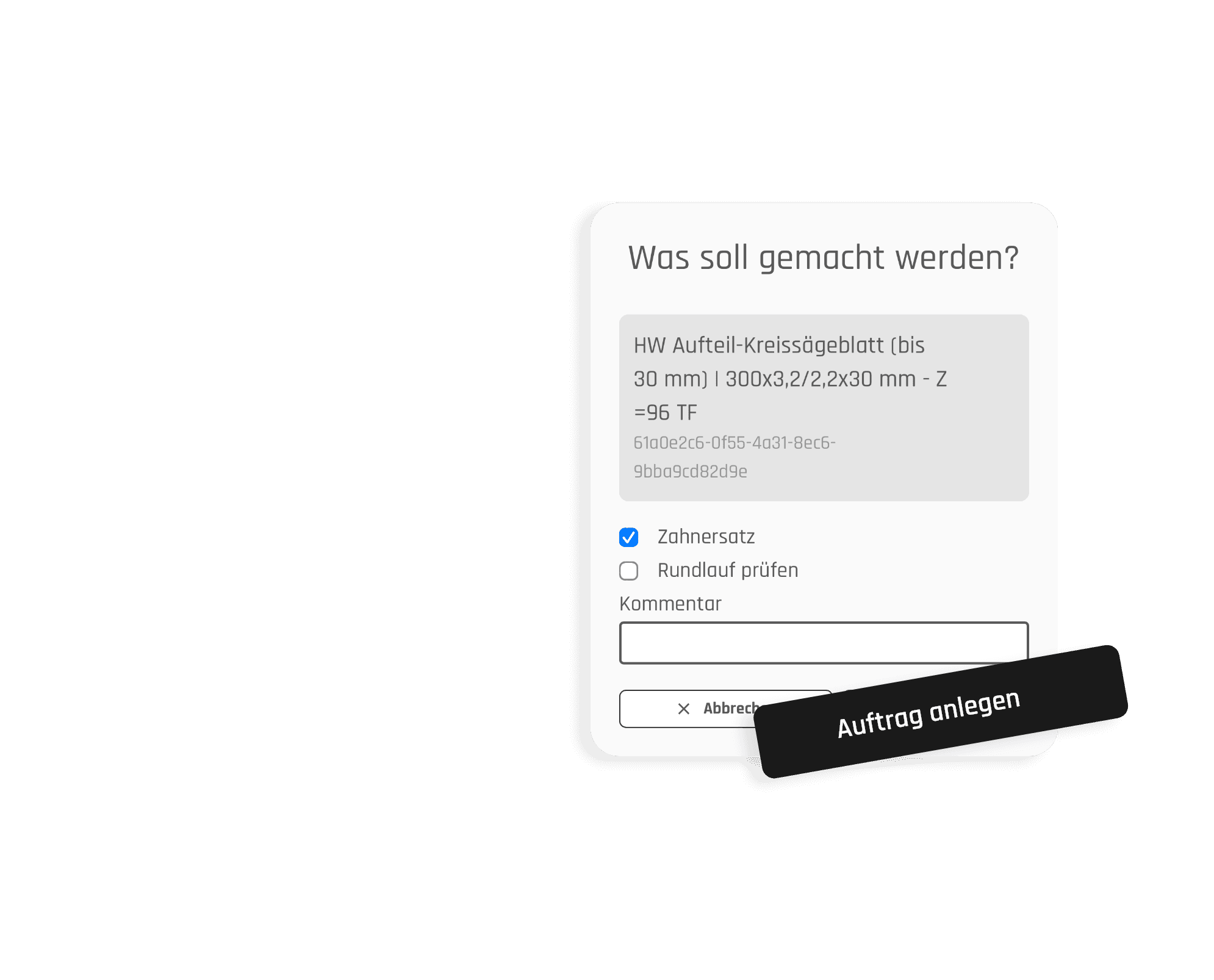
Sharpen tools
Sharpening made digital
Tool maintenance made easy: Select a sharpening service in twinio, create orders and track the process. The new measurement data is available to you immediately after sharpening. Rediscover efficiency.
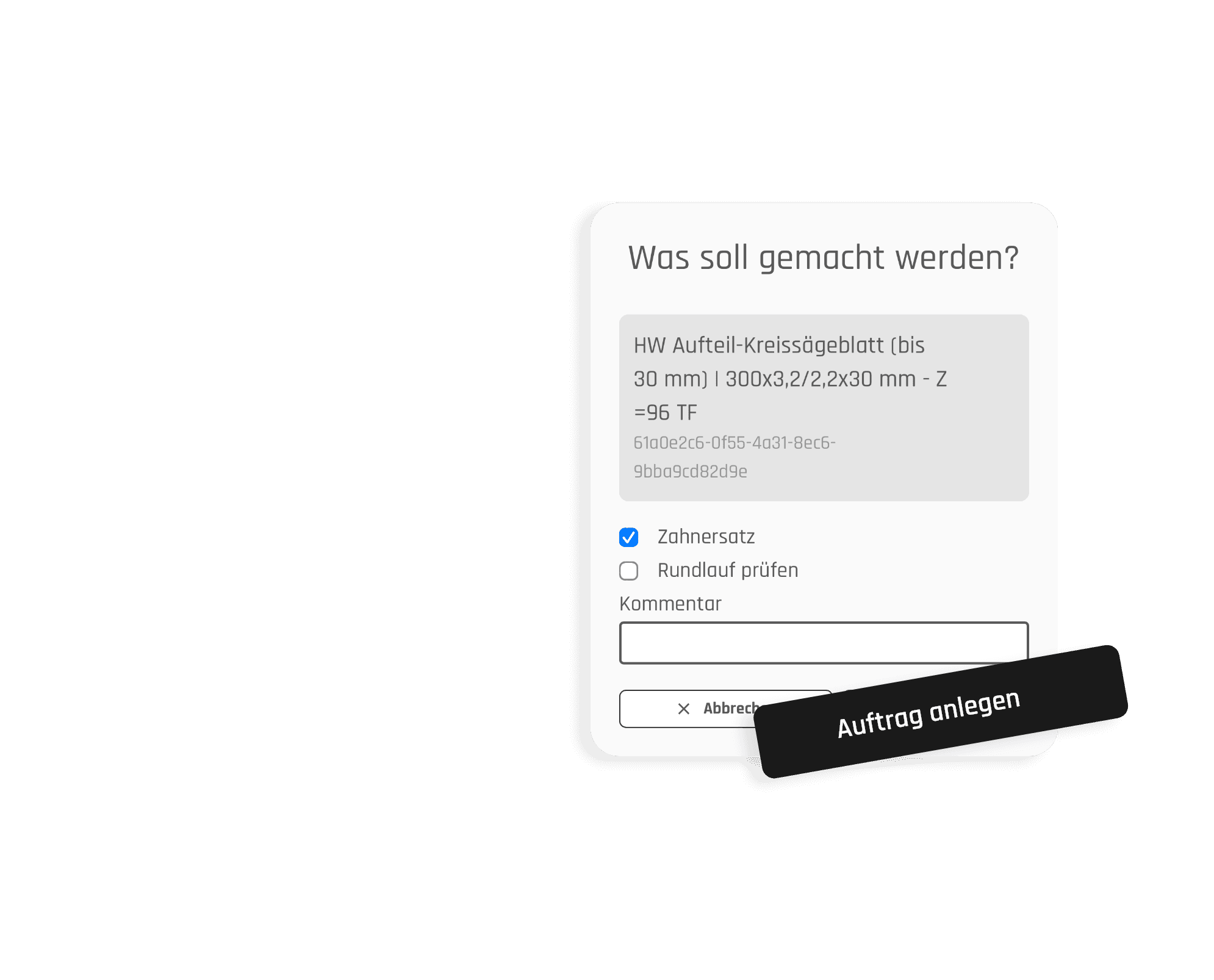
Web app
No matter when and where - directly in the browser
Thanks to the technical implementation as a web app, twinio can be used independently of the device anytime and anywhere in the browser, without any updates being required[1].
Web app
No matter when and where - directly in the browser
Thanks to the technical implementation as a web app, twinio can be used independently of the device anytime and anywhere in the browser, without any updates being required[1].
Web app
No matter when and where - directly in the browser
Thanks to the technical implementation as a web app, twinio can be used independently of the device anytime and anywhere in the browser, without any updates being required[1].
Prices
Prices
Prices
Choose the right
package for your
tool management
Basic
Yearly
7.50
€
Per month
Unlimited number of users
Unlimited number of tools
Custom QR codes
Capture process data manually
Basic
Yearly
7.50
€
Per month
Unlimited number of users
Unlimited number of tools
Custom QR codes
Capture process data manually
Basic
Yearly
7.50
€
Per month
Unlimited number of users
Unlimited number of tools
Custom QR codes
Capture process data manually
Basic + Scanning
Yearly
11.67
€
Per tool partner / per month
Unlimited number of users
Unlimited number of tools
Custom QR codes
Capture process data manually
Scan unique manufacturer IDs & uniquely identify
Basic + Scanning
Yearly
11.67
€
Per tool partner / per month
Unlimited number of users
Unlimited number of tools
Custom QR codes
Capture process data manually
Scan unique manufacturer IDs & uniquely identify
Basic + Scanning
Yearly
11.67
€
Per tool partner / per month
Unlimited number of users
Unlimited number of tools
Custom QR codes
Capture process data manually
Scan unique manufacturer IDs & uniquely identify
Basic + Sharpening
Yearly
15.00
€
Per sharpening service / per month
Unlimited number of users
Unlimited number of tools
Custom QR codes
Capture process data manually
Create and track sharpening orders
Basic + Sharpening
Yearly
15.00
€
Per sharpening service / per month
Unlimited number of users
Unlimited number of tools
Custom QR codes
Capture process data manually
Create and track sharpening orders
Basic + Sharpening
Yearly
15.00
€
Per sharpening service / per month
Unlimited number of users
Unlimited number of tools
Custom QR codes
Capture process data manually
Create and track sharpening orders
Plus Scanning + Sharpening
Yearly
19.17
€
For sharpening service & tool partner
Unlimited number of users
Unlimited number of tools
Custom QR codes
Capture process data manually
Scan unique manufacturer IDs & uniquely identify
Create and track sharpening orders
Plus Scanning + Sharpening
Yearly
19.17
€
For sharpening service & tool partner
Unlimited number of users
Unlimited number of tools
Custom QR codes
Capture process data manually
Scan unique manufacturer IDs & uniquely identify
Create and track sharpening orders
Plus Scanning + Sharpening
Yearly
19.17
€
For sharpening service & tool partner
Unlimited number of users
Unlimited number of tools
Custom QR codes
Capture process data manually
Scan unique manufacturer IDs & uniquely identify
Create and track sharpening orders
Connect
Lets talk!
One-time costs per machine on request
Unlimited number of users
Unlimited number of tools
Custom QR codes
Capture process data automatically
Machine connectivity with selected machine
Automatic transfer of tool data to the machine
Access to the cloud-based tool database of the machine
Connect
Lets talk!
One-time costs per machine on request
Unlimited number of users
Unlimited number of tools
Custom QR codes
Capture process data automatically
Machine connectivity with selected machine
Automatic transfer of tool data to the machine
Access to the cloud-based tool database of the machine
Connect
Lets talk!
One-time costs per machine on request
Unlimited number of users
Unlimited number of tools
Custom QR codes
Capture process data automatically
Machine connectivity with selected machine
Automatic transfer of tool data to the machine
Access to the cloud-based tool database of the machine
News
News
News
New in twinio
Blog
Blog
Blog
Tool management made digital and efficient from practice
FAQ
How do I get twinio on my smartphone?
How do I get twinio on my smartphone?
How do I get twinio on my smartphone?
How do I add tools and recordings to twinio Mobile?
How do I add tools and recordings to twinio Mobile?
How do I add tools and recordings to twinio Mobile?
How do I change the location of a tool in twinio Mobile?
How do I change the location of a tool in twinio Mobile?
How do I change the location of a tool in twinio Mobile?
How do I set limit values for my tool in twinio Mobile?
How do I set limit values for my tool in twinio Mobile?
How do I set limit values for my tool in twinio Mobile?
How do I manually sharpen tools in twinio Mobile?
How do I manually sharpen tools in twinio Mobile?
How do I manually sharpen tools in twinio Mobile?
How do I create a QR code for my tool?
How do I create a QR code for my tool?
How do I create a QR code for my tool?
How do I connect tools and adapters in twinio Mobile?
How do I connect tools and adapters in twinio Mobile?
How do I connect tools and adapters in twinio Mobile?
More questions?
Matching solutions

materialManager
Manage material digitally

materialManager
Manage material digitally

materialManager
Manage material digitally

productionManager
Digital job folder

productionManager
Digital job folder

productionManager
Digital job folder

ServiceBoard
Remote and digital machine service

ServiceBoard
Remote and digital machine service

ServiceBoard
Remote and digital machine service
Get started
with twinio now
Now get started with
twinio
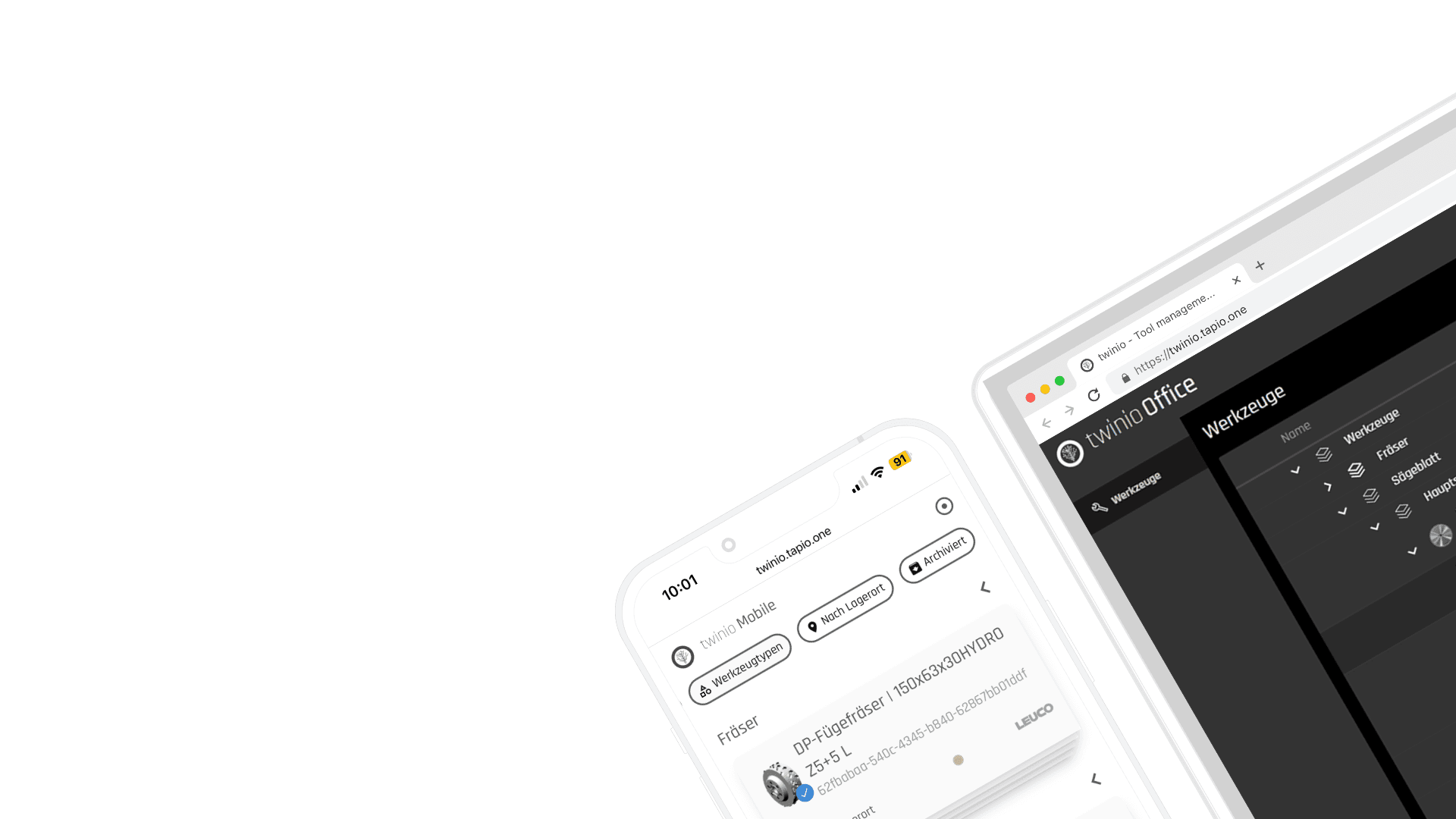
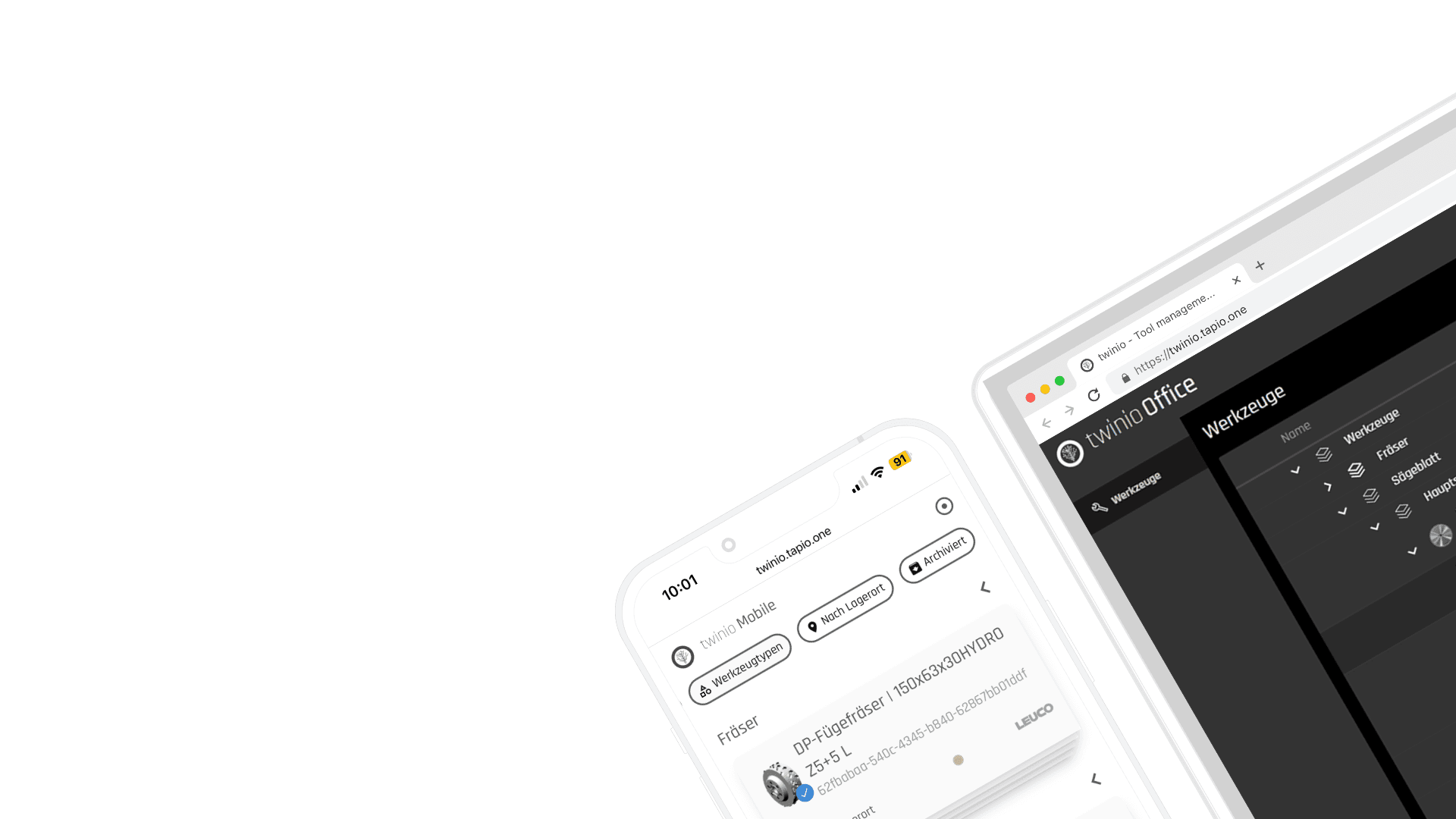
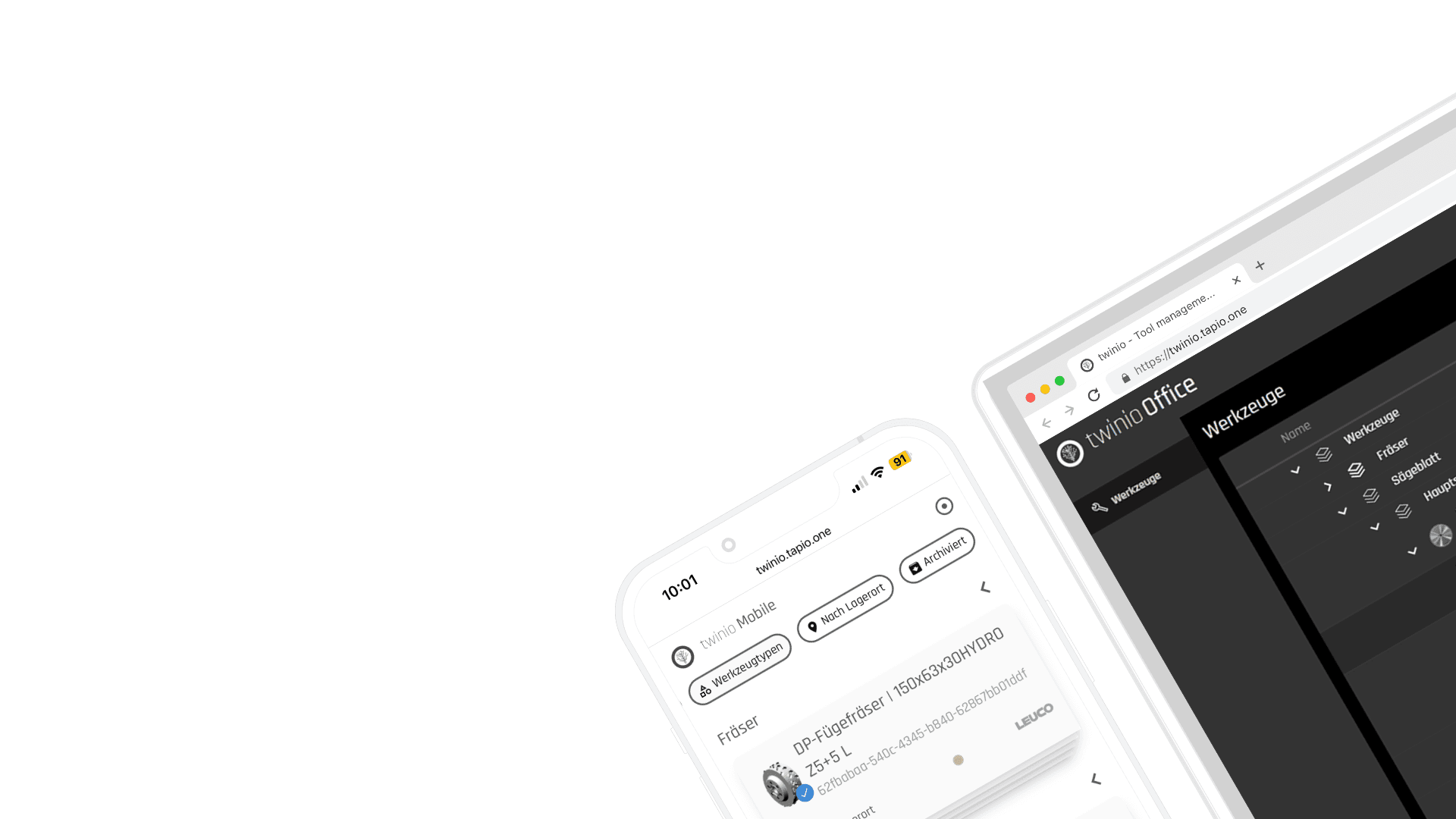
Use twinio on your smartphone or computer and log in to My tapio to take advantage of easy tool management across all your devices.
Use twinio on your smartphone or computer and log in to My tapio to take advantage of easy tool management across all your devices.
No My tapio company account yet?
No My tapio company account yet?
No My tapio company account yet?