Blog
Blog post by our guest: IfW implements an IoT platform
Tuesday, January 26, 2021

Kamil Guezel & Matthias Schneider (ifW)
IfW implements an IoT platform for digitizing woodworking.
The ever advancing digitization and automation in the industry offer new possibilities for networked and intelligent work. Following this approach, in the course of a trilateral "Industry 4.0" project, the processing machines at the Institute for Machine Tools (IfW) of the University of Stuttgart were made fit for a SmartLab ("Digital Wood Lab") using an IoT platform. This makes it possible to bring together various data sets related to each other using intelligent analysis methods to conclude the respective machine states and, thus, about the manufacturing process, and derive forecasts. The basis for this transformation is the cloud-based technology platform of tapio GmbH and the central data acquisition unit of Schneider Electric SE.
The Internet of Things (IoT) and the establishment of cyber-physical systems enable machines, plants, and their components to communicate with each other and with machine operators via the industrial Internet. This development is driven, among other things, by the cost-effective production and miniaturization of sensors so that the increased use of physical sensors in production is greatly facilitated. The trend toward digital transformation requires the establishment of communication structures to expand data exchange in the manufacturing industry and research and education.
To advance the digitization of the test field at the IfW, a central data acquisition unit was installed that collects data from various measuring stations, processes it, and makes it viewable via different output media. For this purpose, sensor technology was implemented to acquire climate data in the test field and the control of limit values so that environmental influences on machines and plants can be monitored. Power meters are used to determine energy consumption at the central sawdust extraction system and at the CNC machining centers to conclude capacity utilization. This is necessary because there is otherwise no other way of recording power consumption at the existing machines.
The connection of inventory machines to IoT was implemented using the BrownField approach. The solutions presented here are based on the ecosystem of tapio GmbH. Although they were designed specifically for the test field at IfW, they can also be transferred to industrial production with appropriate adaptations.

Figure 1: The data flow of the "digital wood lab" at IfW.
Figure 1 schematically illustrates the implementation of digital woodworking at the institute. The machine and sensor data are written to an OPC UA server in the form of OPC UA items to be read by a cloud connector. This cloud connector transfers the data to the digital ecosystem. There, this data is then available for various applications. In the SmartLab, the MachineBoard, as an application from tapio, was used as an example. The MachineBoard runs as an app on mobile devices (smartphones, tablets, smartwatches, etc.) and visualizes the information about the processing machines and the test field. Here's more to read about the MachineBoard.
GreenField vs. BrownField
A fundamental distinction is made between the two approaches in connection with digital transformation. First, the GreenField approach is based on planning an ideal, fully digitized production site, without preconditions through existing machines or plants, on a symbolically free, green field. In most cases, however, a production site is already in operation, so it corresponds more to, secondly, a brownfield that has already been cultivated. In such cases, potentially unsuitable machinery and equipment cannot only be replaced, nor can the production process be interrupted for an extended period. Therefore, the focus lays on the BrownField approach that is equally adapted to the given setup and the desired architecture. In this context, the digitization concept at the IfW was also implemented according to the BrownField approach. A network of sensors was placed over existing processing machines to make them "cloud-ready" in this alternative way. This prevented intervention in the existing plant technology to retain the existing operator permission of the machines.
By collecting large amounts of data in the IoT platform, it is possible to relate this data to each other to draw process- and machine-relevant conclusions and derive forecasts. Such forecasting tools aim to increase the plants' productivity and reduce downtimes, e.g., with the predictive maintenance approach, which is made possible in particular by the use of the DashBoard and the option of displaying historical data in the form of statistics and charts available with it.
The hardware of the IoT platform
The central data acquisition unit from Schneider Electric SE, which forms the basis for retrieving sensor and machine data, is shown in Figure 2. A switched-mode power supply is used to regulate the input voltage from 230 V AC to 24 V DC. The 24 V DC voltage network supplies the programmable logic controller (PLC), the industrial PC (iPC), and the test field's sensor technology. Analog and digital input modules are connected to the PLC for the connection of the sensors. An analog input module provides four analog inputs with measurement inputs 4 - 20 mA, 0 - 20 mA, 0 - 10 V, -10 - 10 V, and various options for connecting thermocouples or temperature probes. A digital input module provides sixteen input channels with 24 V DC input voltage. Currently, up to fourteen modules can be connected to the PLC. The OPC UA server is located on the PLC, which passes the sensor data to a tapio CloudConnector. The machines' energy data are recorded via additional energy meters in the machines and forwarded to the PLC via a bus system (Modbus). Besides, the PLC is connected to an iPC, making the Cloud Connector available and via which the Cloud Connector can be configured.
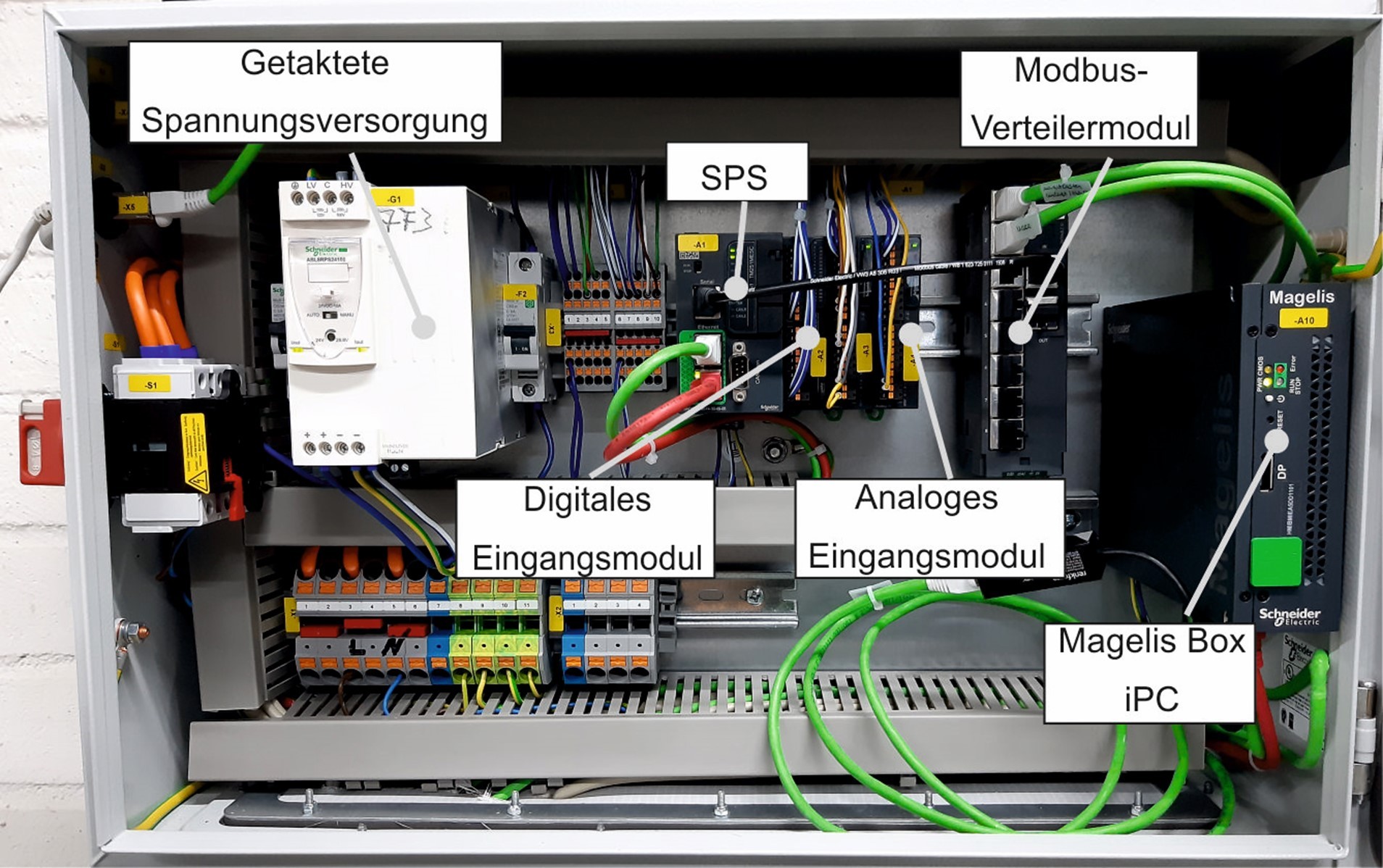
Figure 2: Central control unit with the modules for data acquisition.
Software for data exchange
Machines with a communication interface (Ethernet Adapter Local Area Connection), as is the case with the PRO-MASTER 7017 machining center already present at the institute, allow machine data to be read directly from the controller. To implement the communication between the machine and the cloud, the software Node-RED was used. Node-RED is a graphical development tool from the IBM company. So-called "nodes" are linked to form a "flow" by drawing connections so that data can be processed, and thus simple use cases from the field of IoT can be implemented. Data from sensors, especially those used to monitor machines that are no longer state of the art, could also be related through Node-RED. This serves as the data basis for generating push notifications in the MachineBoard app, for example, to alert the machine operator to current events. In this way, the tapio MachineBoard can visualize information from the sensor and machine data in real-time for the app's machine operators. The user himself selects in tapio which of his data is made available for which application. This guarantees that the user himself remains the master of his data. A particular advantage of the digital ecosystem is the realization of the BrownField approach: The possibility of integrating and connecting existing machines, systems, and sensors from different manufacturers and suppliers in terms of data technology digitally maps the physical diversity of production. Due to data provided in a central location, a good overview of all machines, tools, and materials connected in the digital ecosystem results. If this data is used for the MachineBoard app, for example, more flexibility is enabled in daily work because a machine operator can always be at the right machine or plant at the right time. In general, errors, warnings, and actions for machines and plants are determined in real-time and passed on to mobile devices through the cloud solution.
The benefits of tapio's ecosystem are not only evident in the MachineBoard application. Other software services are already available through tapio as well. Thus, the data provided in the tapio ecosystem can also be used for tool management, digital machine service, cutting optimization, and to display historical production data. Data from production comes together in tapio, which can be used for various applications from different suppliers, such as the cutting optimization intelliDivide from HOMAG.
Implemented solutions in the test field
Figure 3 shows an example of a screenshot of the tapio MachineBoard for a processing center. A correspondingly assigned color expresses the respective machine status in the upper right field. The green color corresponds to the "producing" state of the processing machine. Also, the actual speed and the target speed of the spindle, the spindle load, as well as the tool ID, and the radius of the current tool clamped in the spindle have been implemented.
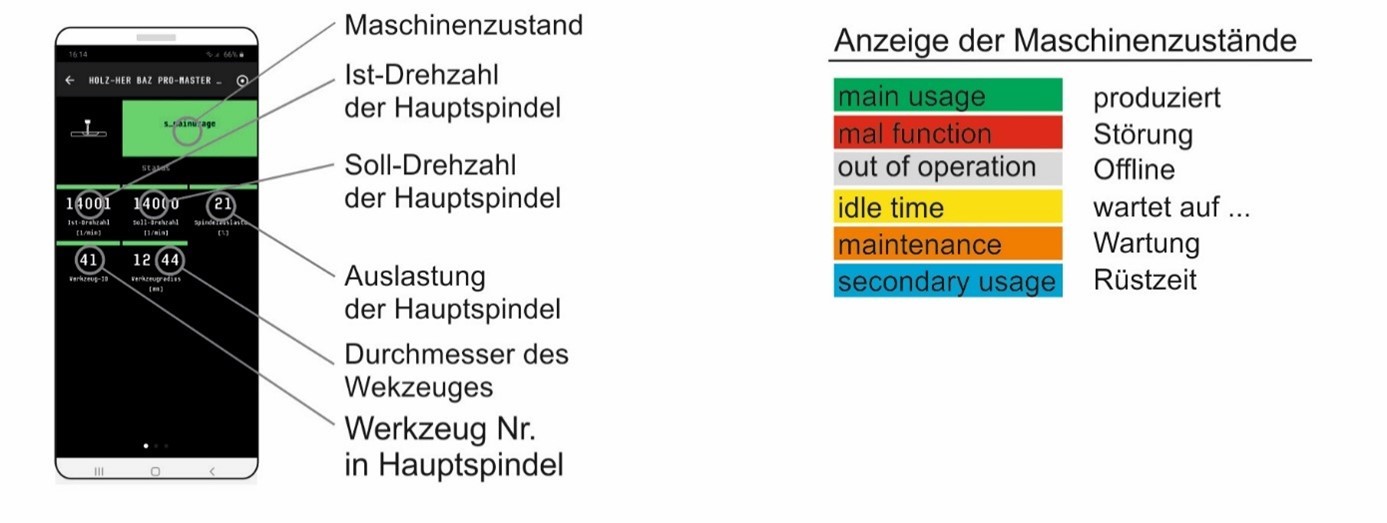
Figure 3: MachineBoard as an interface for visualizing the variables of a machine control system.
The information on the tools in the magazine of a machine in the form of the ID is particularly well suited for implementing simplified tool management, as this can be used above all in the context of predictive maintenance to make predictions on the wear of a tool. This data can be compared with the performance data of a machine and analyzed for correlations to ensure the optimum utilization or service life of tools.
When machining materials that can swell or shrink, the surrounding space's temperature and humidity play a significant role, for this reason, the climate data in the test field are recorded and visualized for consideration during test runs. In deviating test results, the temporal course of the climate data in the cloud can be viewed and displayed retroactively on the dashboard. In contrast to the MachineBoard, the dashboard is an instrument that serves to display historical data over a desired period.
The particular strength of the solution implemented at the IfW is that the machines and systems already implemented can be supplemented by many additional machines and test benches in the test field on the one hand and additional sensors and actuators on the other. Thus, the test field's digitization can be flexibly adapted and extended to changing requirements, for example, in test runs. For any application, it is possible to select sensors or read data directly from the machine. In contrast to industrial production, the focus of the project described here is not increasing productivity but on determining primary data such as spindle utilization, the difference between actual and target speed, machine condition, etc.. The focus is also on testing the IoT platform and generating new knowledge, from which industrial production can, in turn, derive its benefits.
The test field's digital interface is located in the entrance area of the research departments for wood and composite material processing. Figure 4 shows the central point of the "digital wood laboratory". Here, all the data obtained is visualized and can be made available directly to employees and visitors' mobile devices.
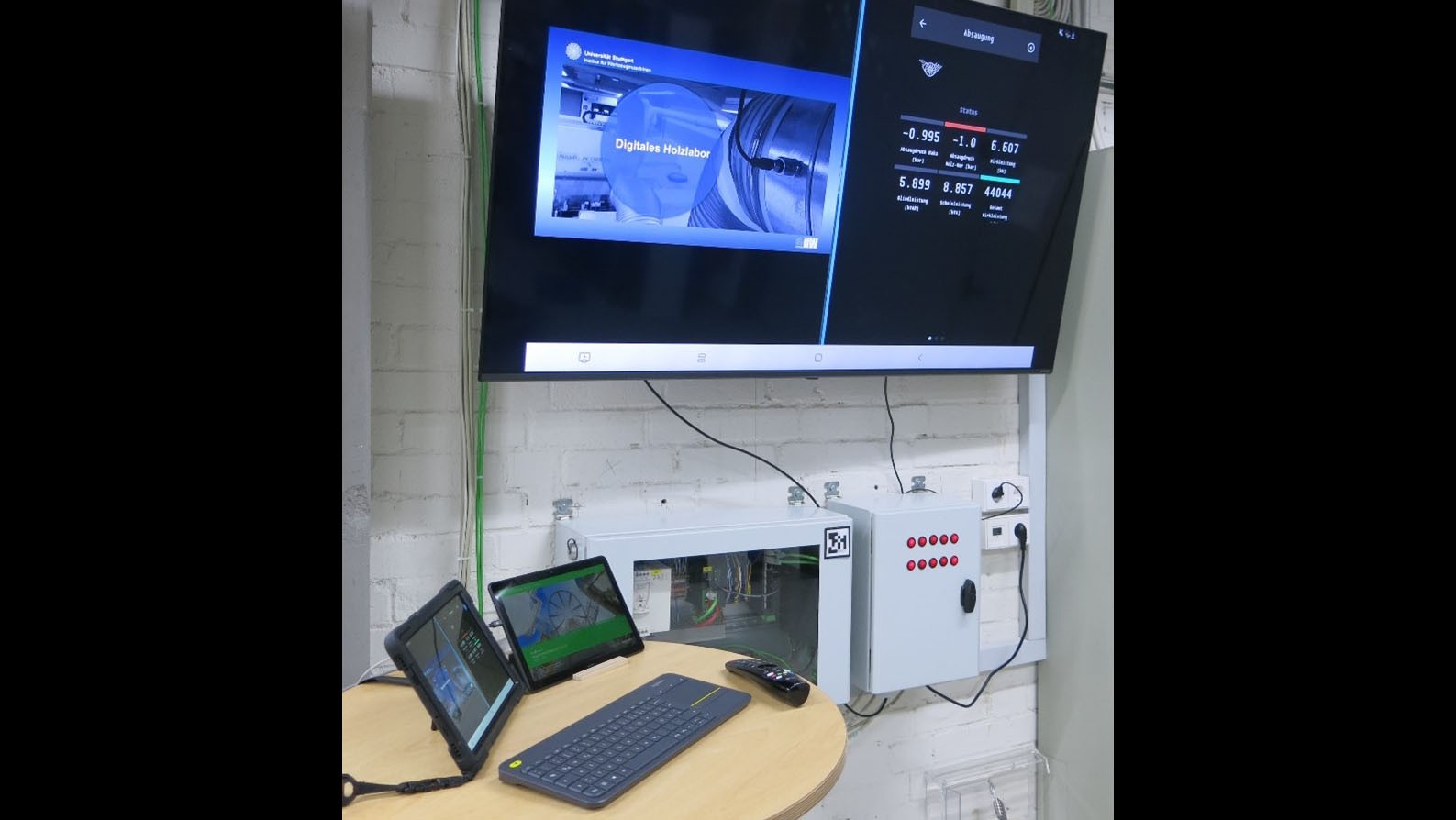
Figure 4: Digital node in the woodworking test field.
Acknowledgments
We want to thank the companies tapio GmbH and Schneider Electric SE for their previous and continuing support in implementing the BrownField approach to digitizing the experimental laboratory at IfW.
Dipl.-Ing. Kamil Güzel
Gruppenleiter Holzbearbeitung Tel.: +49 711 685 84537 e-mail: kamil.guezel@ifw.uni-stuttgart.de
Dipl.-Ing., Pat.-Ing. Matthias Schneider
Gruppenleiter Verbundwerkstoffbearbeitung Tel.: +49 711 685 82396 e-mail: matthias.schneider@ifw.uni-stuttgart.de
Institut für Werkzeugmaschinen Universität Stuttgart Holzgartenstr. 17 D-70174 Stuttgart
www.ifw.uni-stuttgart.de
Many thanks to Kamil Güzel and Matthias Schneider for sharing their insights and valuable learnings in this guest post in our tapio blog.